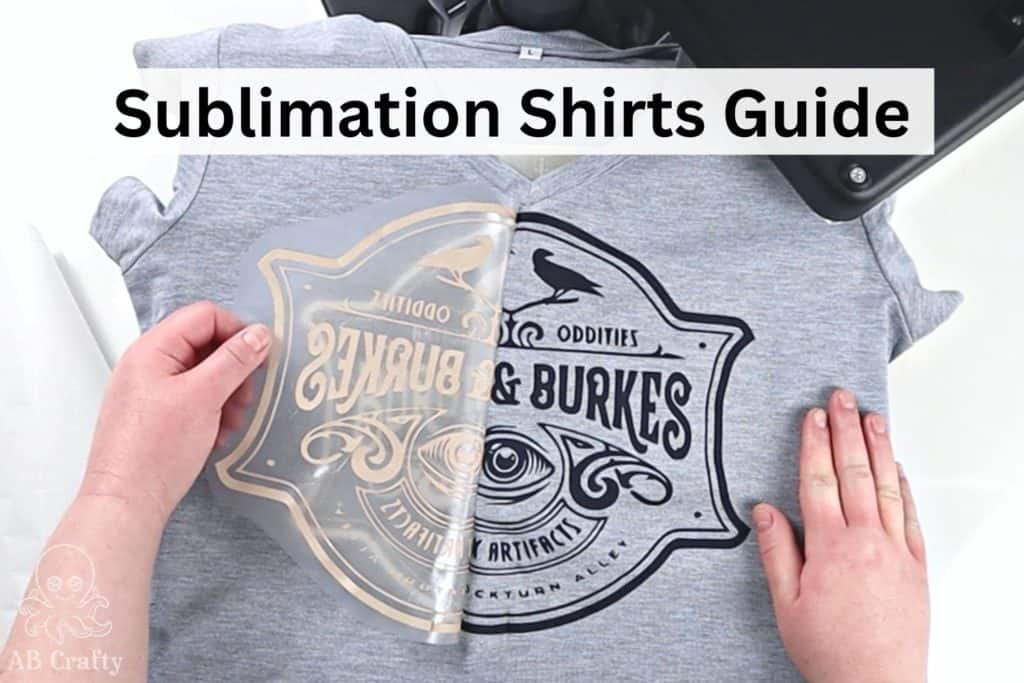
Make perfect sublimation shirts every time with this easy to follow guide. Also learn which shirts are best for sublimation.
Table of Contents
Note: Some links in this post may contain affiliate links, which means at no cost to you, I may earn a commission.
One of my new recent obsessions is making sublimation shirts. I was sent a bunch of products to test out and have been hooked with sublimation ever since. The first thing I made with my heat press and Xtool is a shirt, cutting out a design from infusible ink. It’s a great first project and introduction into sublimation shirts so figured it’s perfect for a beginner guide.
So if you’ve ever wanted to make your own custom clothing pieces, now you can! Whether it’s for yourself or someone special, designing your very own t-shirt with pictures or just words that highlight what makes you unique is a fun way to express yourself. This guide will walk you through the process of sublimation shirt making. I’ll cover what sublimation is and how it works, which shirts are best for sublimation, and finally the step-by-step tutorial on how to make sublimation shirts using infusible ink or sublimation paper. You’ll find everything you need to know about crafting beautiful personalized garments!
And if you want to make your own designs, you can make your own sublimation printer and use sublimation ink.
Get the latest DIY tutorials, reviews, and crafting updates
You'll never be spammed and can unsubscribe at any time
What are Sublimation Shirts?
Sublimation shirts are shirts that you can customize with text or graphics that are dyed directly into the shirt so that you can’t feel them. You can cut or print your design using sublimation ink and then use a heat press to infuse the ink directly into the fabric, dyeing it. Therefore unlike other methods of customizing shirts, using sublimation means you can’t feel the design on top of your garment. This also means your designs won’t crack or fade over time.
Which Shirts are Best for Sublimation?
When it comes to sublimation shirts, the most important factor is choosing the right t-shirt material. The best sublimation shirt materials are 100% polyester, but you can also use a polyester blend. Make sure that you’re using at least 60% polyester, but know that even at 60% the color won’t be as vibrant.
The fabric not only needs to be able to withstand the heat of the sublimation process, but also you want to use material that will give you the most vibrant color. Therefore lighter colors will allow your design to show up best. If you’re using color in your design, a white shirt will give you best outcome. The main thing to keep in mind is the color of the shirt will affect the color of your design. Similarly, the darker the color will make your design pop less.
These are some great options of 100% polyester shirts:
- Cricut Sublimation Crew Neck
- Cricut Women’s V Neck (this is the one I used, but in white)
- Hane’s Cool Dri Crew Neck
- Hane’s Cool Dri Women’s V Neck
There are ways to use sublimation on cotton shirts, non-polyester shirts, and colored shirts, but that requires either DTF or sublimation paper specifically for cotton and uses a different process.